When machines move, bearings make it happen smoothly. From tiny gadgets like fans to massive industrial equipment, bearings are everywhere — and choosing the right one isn’t just a technical detail. It directly affects performance, efficiency, and maintenance costs.
Two of the most widely used bearing types are the ball bearing and the roller bearing. While they may seem similar at first glance, they are designed to handle loads and motion in fundamentally different ways. A ball bearing relies on spherical balls and is best suited for light to moderate loads and high-speed applications. On the other hand, a roller bearing uses cylindrical or tapered rollers and is built to withstand heavier loads and rougher operating conditions.
If you’re a design engineer, technician, or plant manager, understanding the differences between these two can help you make more informed decisions — especially when equipment reliability is on the line. A wrong choice can lead to premature wear, downtime, and added costs.
Roller Bearing vs Ball Bearing: What’s the Real Difference?
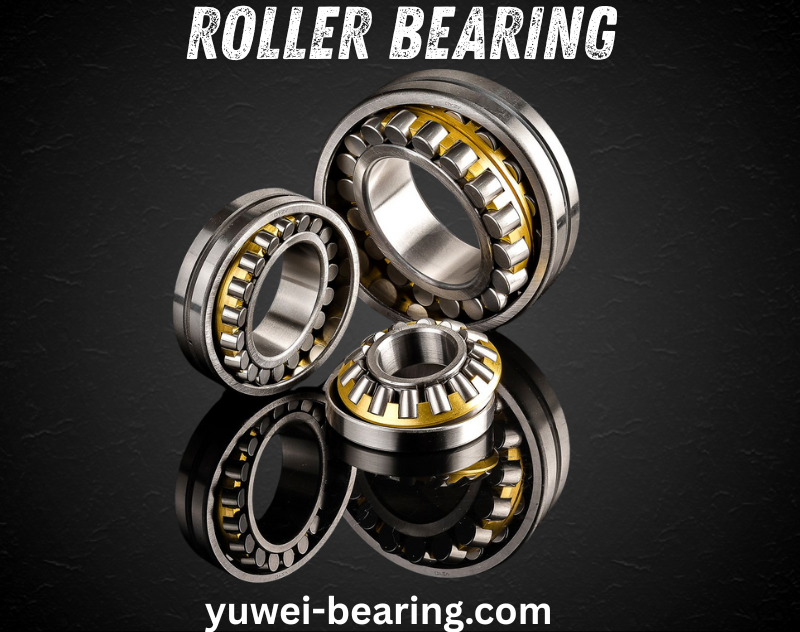
In this guide, we will explain how roller-bearing differ from ball bearings in function, structure, performance, and real-world applications — helping you choose the right bearing for the job.
Understanding the differences between a roller bearing and a ball bearing is essential for selecting the right component in mechanical systems. Both types are designed to reduce friction between moving parts, but they operate differently and are built for different applications. This guide will explain everything in detail. Visit here!
What Is a Bearing, Anyway?
A bearing is a machine element that enables rotational or linear movement while minimizing friction and handling stress. Bearings support rotating shafts and other components, making them fundamental in mechanical assemblies across industries. The primary role of a bearing is to support load and reduce friction, making movement efficient and extending the life of machinery.
There are two main types of rolling element bearings: ball bearings and roller-bearing. While both share similar construction elements (inner race, outer race, and rolling elements), the shape and behavior of the rolling elements make all the difference.
What Is a Ball Bearing?
A ball bearing uses spherical balls as the rolling elements. These balls sit between two smooth surfaces called races (inner and outer), allowing components to rotate with minimal friction.
Key Characteristics of Ball Bearings:
- Point Contact: Balls make point contact with the races, resulting in lower friction and smoother operation.
- Speed Efficiency: Designed for high-speed applications due to low friction.
- Moderate Load Capacity: Best for moderate radial and axial loads.
- Cost-Effective: Generally cheaper than roller-bearing due to simpler construction.
Common Applications:
- Electric motors
- Fans
- Office equipment
- Home appliances
Ball bearings are ideal for situations requiring high-speed performance and light to moderate loads. However, they can deform under heavy loads, which limits their usage in heavy-duty systems.
What Is a Roller-Bearing?
A roller-bearing uses cylindrical or tapered rollers instead of balls. These rollers provide a line contact with the races, distributing the load over a larger area.
Key Characteristics of Roller Bearing:
- Line Contact: Allows better distribution of forces, making them suitable for heavier loads.
- Higher Load Capacity: Can handle greater radial and axial loads than ball bearings.
- Slower Speed: More friction than ball bearings, so they are less suitable for high-speed applications.
- Greater Durability: Better suited for shock and heavy load conditions.
Types of Roller-Bearing:
- Cylindrical: Supports heavy radial loads.
- Tapered: Handles both axial and radial loads.
- Needle: Compact design for limited space.
- Spherical: Accommodates misalignment and shaft deflection.
Common Applications:
- Automotive hubs
- Industrial conveyors
- Gearboxes
- Agricultural machinery
Roller bearings are preferred in industrial environments and heavy machinery where high load handling is essential.
Technical Comparison: Ball vs. Roller Bearing
The differences between ball bearings and roller bearings can be understood more clearly in a side-by-side format.
Feature | Ball Bearing | Roller Bearing |
---|---|---|
Rolling Element | Spherical balls | Cylindrical or tapered rollers |
Contact Area | Point contact | Line contact |
Load Capacity | Moderate | High |
Speed Capability | High | Lower |
Axial Load Handling | Moderate | High (especially tapered) |
Radial Load Handling | Moderate | High |
Misalignment Tolerance | Low | Higher (especially spherical) |
Durability | Moderate | High |
Cost | Lower | Slightly higher |
This technical comparison shows that roller-bearing excel in high-load, low-speed conditions while ball bearings are ideal for high-speed, low-load setups.
Choosing the Right Bearing: Key Factors
To select between a ball bearing and a roller bearing, consider the following:
- Type of Load:
- If you expect high radial or axial loads, choose a roller-bearing.
- For lighter, dynamic loads, a ball bearing may be more efficient.
- Speed Requirements:
- Use ball bearings for high-speed applications.
- Roller-bearing are better suited to slower, heavy-duty operations.
- Alignment Conditions:
- If your system may experience shaft misalignment, go with spherical roller-bearing.
- If precise alignment can be maintained, ball bearings are sufficient.
- Space Constraints:
- Needle roller bearing are ideal where space is tight.
- Ball bearings are also compact and versatile.
- Environmental Factors:
- Roller-bearing handle shock and contaminants better.
- Ball bearings are more sensitive and may require sealed environments.
- Cost vs. Longevity:
- Ball bearings are less expensive initially.
- Roller bearing provide better ROI in heavy-load or high-wear scenarios.
Choosing the right bearing prevents premature failure and reduces maintenance downtime.
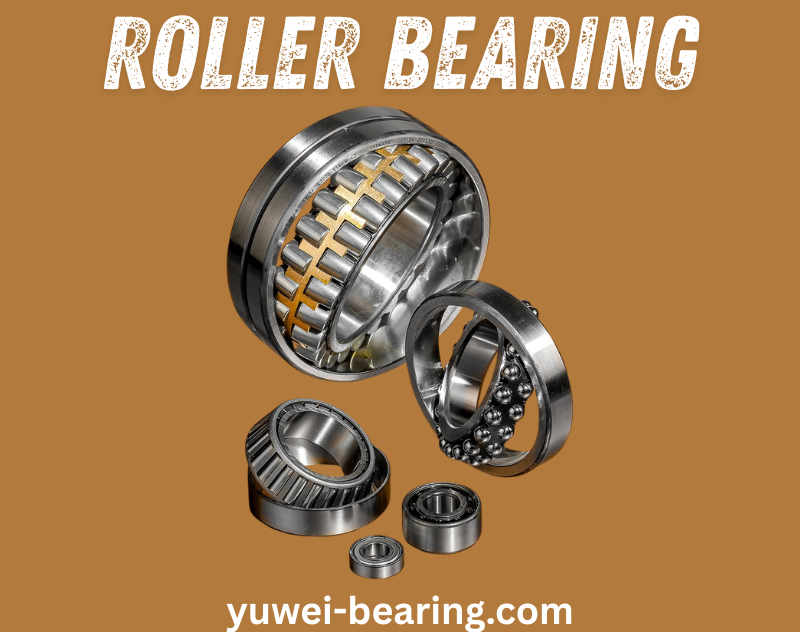
Maintenance and Failure Modes
Understanding how each bearing type behaves under stress helps with preventive maintenance.
Ball Bearing Failure Modes:
- Pitting and Spalling: Caused by point contact stress over time.
- Overheating: From insufficient lubrication at high speeds.
- Cage Failures: If the cage is weak or worn.
- Corrosion: Due to moisture or poor storage.
Roller-Bearing Failure Modes:
- Fatigue Cracks: From repeated high-load cycles.
- Misalignment Damage: Especially if improperly installed.
- Contamination: Can wear down rollers and races.
- Lubrication Failure: Causes excessive wear and heating.
Maintenance Tips:
- Monitor temperature and vibration.
- Ensure proper lubrication.
- Use seals or shields where necessary.
- Check for noise or play in the shaft.
Roller bearings generally last longer under heavy-duty conditions but require consistent maintenance.
Industry Insights: What Experts Say
Mechanical and reliability engineers consistently evaluate bearing types for performance.
According to a 2023 survey by BearingNet:
- 57% of industrial engineers preferred roller-bearing for plant machinery.
- 68% agreed that improper bearing selection is a leading cause of early equipment failure.
- Ball bearings were identified as more suitable for light-duty, high-speed applications like HVAC systems and electronics.
Engineering Tip: When in doubt, analyze load paths and consult the manufacturer’s specification. Roller bearing are often better for industrial environments, while ball bearings perform well in lightweight consumer devices.
Common Myths: Debunked
- Myth: Ball bearings are always better because they’re cheaper.
- Reality: They’re cheaper initially but may wear out faster under stress.
- Myth: Roller bearings are only for heavy machinery.
- Reality: Many mid-load systems also benefit from the added durability.
- Myth: All bearings are interchangeable.
- Reality: Choosing the wrong bearing affects efficiency and may lead to breakdowns.
- Myth: Roller bearings can’t run fast.
- Reality: Some designs like cylindrical rollers do manage moderate speeds efficiently.
- Myth: Lubrication isn’t important.
- Reality: Both types need proper lubrication to prevent overheating and wear.
Educating teams on bearing myths can reduce errors in engineering design and maintenance.
Final Verdict: When to Use Which
Application Area | Recommended Bearing |
High-speed electric motors | Ball bearing |
Automotive axles | Tapered roller-bearing |
Misaligned shafts | Spherical roller-bearing |
Compact industrial machines | Needle roller-bearing |
General low-load rotation | Ball bearing |
Heavy conveyor belts | Cylindrical roller-bearing |
General Rule of Thumb:
- Use ball bearings for lighter, faster applications with consistent alignment.
- Use roller-bearing when strength, load capacity, and durability are more critical than speed.
Proper selection of a roller bearing over a ball bearing (or vice versa) isn’t about what’s better overall — it’s about what’s better for your specific use case.
Q&A Section
Q1: Can I replace a ball bearing with a roller-bearing directly?
A1: Not always. The housing and shaft size may differ. Always consult equipment specs.
Q2: Why do roller-bearings last longer under load?
A2: They have line contact, which distributes force better, reducing stress concentration.
Q3: Which bearing is easier to install?
A3: Ball bearings are generally easier and quicker to install due to simple construction.
Q4: Are roller-bearings noisier?
A4: They can be under poor lubrication or misalignment, but properly installed ones run smoothly.
Q5: Do roller-bearings need more maintenance?
A5: Yes, especially in dirty or high-load environments. Regular checks help extend life.
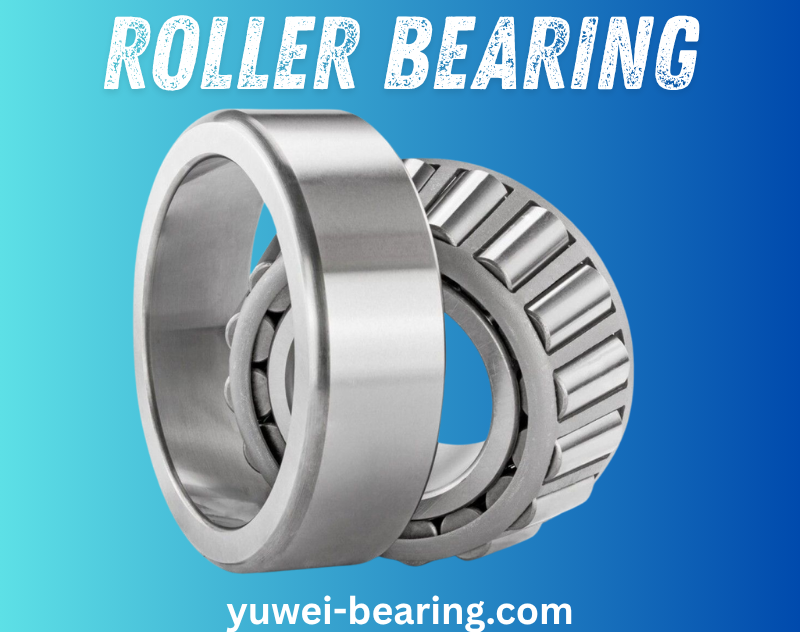
Conclusion
Choosing between a roller bearing and a ball bearing isn’t about which one is better — it’s about which one fits the job. Both serve the same purpose: reducing friction and supporting motion. But the way they handle loads, speeds, and operating conditions is entirely different.
Ball bearings are excellent for light-duty, high-speed applications where space and precision matter. They’re widely used in electric motors, fans, and consumer electronics. Roller bearings, on the other hand, are built for strength. Their line contact design allows them to carry heavy radial and axial loads, making them ideal for automotive, industrial, and high-load machinery.
Understanding these differences helps avoid costly errors in design, operation, and maintenance. It also allows you to improve equipment performance and extend service life by matching the right bearing type to the right task.
Whether you’re replacing components, designing a new system, or maintaining heavy equipment, always factor in load type, speed, alignment, and environment before deciding.