In high-speed industrial environments, every fraction of a second—and every micron of accuracy—matters. Whether you’re running CNC machines, robotic arms, turbines, or medical instruments, consistent performance hinges on components that can handle speed, stress, and precision. One such component that often goes unnoticed but plays a critical role is the precision bearing.
Unlike standard bearings, precision bearing are engineered to operate with ultra-tight tolerances, reduced friction, and exceptional durability under demanding conditions. They’re not just about enabling rotation—they directly impact the accuracy, efficiency, and lifespan of high-speed equipment. When bearings underperform, the entire machine feels it: heat builds up, vibration increases, and product quality suffers.
Over time, this leads to costly downtime, increased maintenance, and inconsistent output—all of which eat into your bottom line. That’s why precision-bearing aren’t a luxury—they’re a necessity for any operation that values speed, reliability, and performance.
In this guide, we will explain how precision-bearing enhance equipment efficiency, what makes them different, where they’re used, and how to choose the right one for your application.
Precision Bearing Enhances Efficiency of High-Speed Equipment
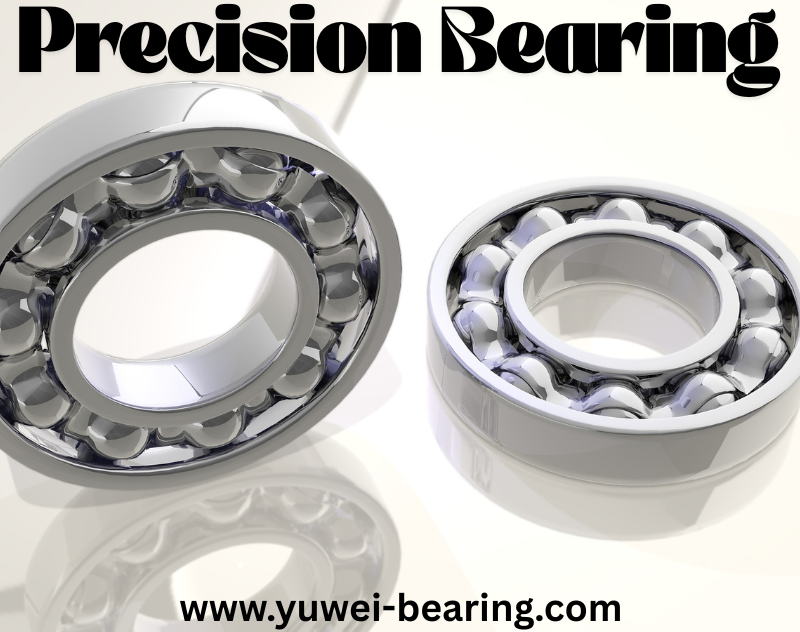
High-speed equipment is the backbone of modern manufacturing, robotics, aerospace, and advanced medical systems. These machines rely on components that can withstand extreme speeds, high loads, and tight tolerance requirements. One such component is the precision-bearing. Often overlooked, precision bearing play a pivotal role in determining machine efficiency, accuracy, and longevity. By reducing friction, heat generation, and vibration, these high-performance bearings help systems run faster and more reliably. This guide provides a comprehensive overview of how precision bearing enhance the efficiency of high-speed equipment. Visit here!
What Is a Precision-Bearing?
Precision bearing are specially designed rolling-element bearings built with extremely tight manufacturing tolerances. They support the rotation of components while minimizing runout (wobble), friction, and heat. Typically rated by standards like ABEC (Annular Bearing Engineers Committee), higher-grade precision-bearing offer better alignment, smoother rotation, and greater speed capabilities compared to standard bearings. They come in various types such as angular contact ball bearings, cylindrical roller bearings, and hybrid ceramic bearings.
How Precision-Bearing Improve High-Speed Equipment Efficiency
1. Reduced Friction and Heat High-speed machines produce significant rotational energy. If the bearing components aren’t precise, more friction is generated, converting kinetic energy into heat. Precision bearing are made with highly polished races and rolling elements that reduce this friction. Less friction means less energy loss and reduced need for cooling systems.
2. Tighter Dimensional Tolerances Precision-bearing are manufactured with tolerances as low as ±0.0001 inches. This minimizes shaft play and ensures perfect alignment. As a result, the equipment can operate at higher speeds without vibration or imbalance, improving performance and reducing maintenance cycles.
3. Improved Load Distribution In high-speed environments, uneven load distribution leads to wear and failure. Precision-bearing maintain consistent contact patterns, distributing axial and radial loads evenly. This enhances stability and extends bearing life.
4. Higher RPM Capabilities Standard bearings max out around 6,000 to 8,000 RPM. Precision-bearing, depending on the type, can exceed 20,000 RPM. Some hybrid ceramic bearings reach over 100,000 RPM. This enables high-speed tools to function at optimal speed without performance degradation.
5. Reduced Vibration and Noise Imbalanced bearings generate micro-vibrations that compromise machining quality. Precision bearing eliminate this with uniform ball/raceway surfaces and strict concentricity. This not only enhances product quality but also reduces noise levels in manufacturing floors.
6. Longer Service Life Precision-bearing resist wear better due to high-grade materials and superior finishes. With better load distribution and less friction, they often last 2-5 times longer than standard bearings, reducing downtime and maintenance costs.
Types of Precision-Bearing
Bearing Type | Description | Common Applications |
---|---|---|
Angular Contact Bearings | Support both axial and radial loads at high speeds | CNC machines, spindles |
Cylindrical Roller Bearings | Offer high radial load capacity and speed | Turbines, compressors |
Hybrid Ceramic Bearings | Combine ceramic balls with steel races for high RPM and low heat | Robotics, medical tools |
Tapered Roller Bearings | Handle heavy combined loads with axial alignment | Gearboxes, axles |
Deep Groove Ball Bearings | Versatile and support moderate speeds | Electric motors, fans |
Advantages of Using Precision-Bearing
- Higher Speed Ratings: Capable of operating at speeds 2-3x that of general-purpose bearings.
- Energy Efficiency: Lower friction reduces energy consumption and cooling demands.
- Consistency in Output: Reduced vibration ensures better product quality and dimensional accuracy.
- Lower Maintenance Requirements: Extended service intervals reduce equipment downtime.
- Compact and Lightweight: High performance in smaller packages helps reduce overall equipment footprint.
Choosing the Right Precision-Bearing
When selecting a precision-bearing for high-speed equipment, consider the following:
- Speed Requirements: Match the bearing’s speed rating (RPM) with your machine’s operating speed.
- Load Conditions: Know the axial, radial, or combined loads and choose the right type accordingly.
- Temperature Range: Bearings must withstand the operational temperature without thermal degradation.
- Lubrication: Choose appropriate grease or oil to reduce friction and maintain performance.
- Tolerance Grades: Higher ABEC ratings (ABEC 5, 7, 9) offer better precision for ultra-fast operations.
- Material Selection: Consider ceramic, stainless steel, or hybrid materials based on your use case.
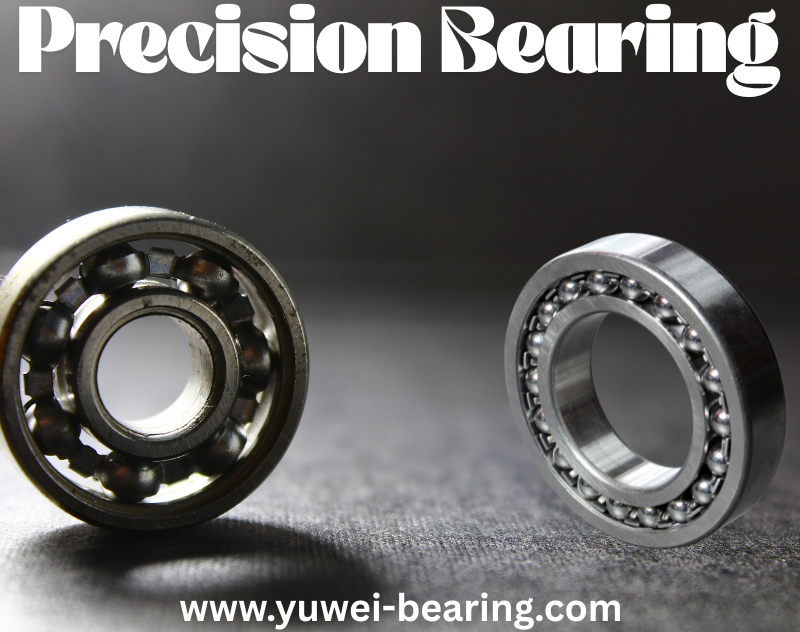
Common Applications of Precision-Bearing
- CNC Spindles: Require ultra-high precision at thousands of RPMs to ensure accurate machining.
- Medical Equipment: Devices like dental drills and MRI machines need quiet, stable, and precise movement.
- Aerospace: Jet engines and actuators use bearings that can withstand extreme loads and temperatures.
- Robotics: Precision-bearing ensure smooth, repeatable motion in robotic joints and arms.
- Semiconductor Fabrication: Extreme precision is essential in wafer positioning and lithography equipment.
Lubrication Guide for Precision Bearing
Proper lubrication is essential for performance and life expectancy. Here’s a simple table to guide you:
Lubrication Type | Best For | Advantages | Notes |
Grease | General use, moderate speed | Easier maintenance | Can increase friction at high RPMs |
Oil | High-speed, low torque | Lower friction, better cooling | Requires sealing or circulation system |
Solid Lubricants | Extreme environments | No leakage, clean | Limited to specific niche applications |
Troubleshooting Precision Bearing Issues
Symptom | Possible Cause | Solution |
Excessive noise | Contamination or misalignment | Clean/replace bearing, realign shaft |
Overheating | Inadequate lubrication | Check and replenish lubricant |
Vibration | Imbalance or wear | Inspect and replace if damaged |
Short lifespan | Overloading or poor installation | Reduce load, review fitting method |
Questions and Answers (Q&A)
Q1: What is the difference between standard and precision-bearing?
A: Precision bearing are built to tighter tolerances and can operate at higher speeds with better stability and less vibration compared to standard bearings.
Q2: Are ceramic bearings always better than steel?
A: Not always. Ceramic bearings perform better at high speeds and low lubrication environments but are more expensive. Steel is sufficient for moderate-speed applications.
Q3: Can I use precision-bearing in retrofitted machines?
A: Yes, many precision bearing are available in standard sizes and can replace older bearings, provided the rest of the system is compatible.
Q4: What ABEC rating should I choose?
A: ABEC 5 is typically sufficient for most high-speed applications. Use ABEC 7 or 9 for ultra-precision requirements like aerospace or semiconductor manufacturing.
Q5: How often should I replace precision-bearing?
A: It depends on the load, speed, and environment. With proper lubrication and installation, they may last 2-5 times longer than standard bearings.
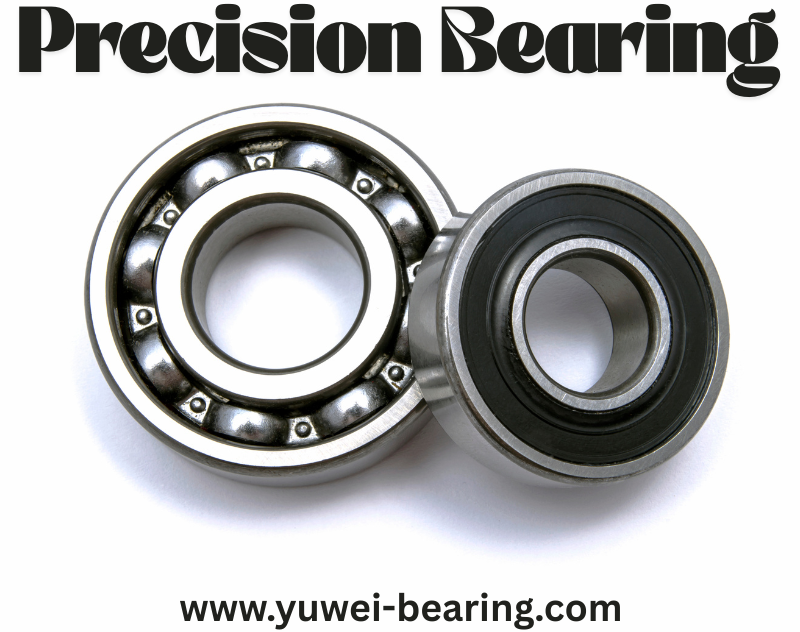
Conclusion
Precision bearing may be small in size, but their impact on high-speed equipment is anything but minor. From reducing friction and vibration to enabling higher RPMs and extending service life, these components play a vital role in maintaining the efficiency, reliability, and output quality of modern machinery. Whether you’re operating in aerospace, robotics, medical manufacturing, or industrial automation, the right bearing can mean the difference between smooth, consistent performance and frequent, costly downtime.
Investing in precision-bearing is not just about preventing breakdowns—it’s about optimizing your entire operation. By choosing bearings with tighter tolerances, better materials, and the right specifications for your load and speed requirements, you ensure your equipment performs at its best with minimal interruption.
Remember, efficiency starts at the core of your machine. Precision bearing provide the foundation for high-speed success, helping you increase productivity, reduce maintenance costs, and deliver higher-quality results to your customers. Whether you’re upgrading existing systems or building new ones, precision-bearing should be a strategic part of your planning.