In the world of industrial machinery, performance and reliability often come down to one small but essential component—the bearing. Whether it’s powering automotive systems, supporting conveyor belts, or enabling high-speed spindles, bearings must perform under pressure, temperature, and load without fail. But consistent performance doesn’t just depend on the bearing itself—it starts with the bearing supplier.
A professional bearing supplier does more than just deliver products. They implement strict quality control processes, use precision manufacturing techniques, and apply industry-specific knowledge to ensure every bearing performs reliably from day one. From selecting raw materials to final packaging and performance testing, each step is designed to meet the highest standards of durability, consistency, and efficiency.
For engineers, procurement teams, and plant managers, understanding what makes a bearing supplier reliable is key to reducing downtime, avoiding costly failures, and improving equipment lifespan. So how can you be sure your supplier is doing it right?
In this guide, we will explain the essential techniques top bearing suppliers use to guarantee high product performance—so you can make smarter sourcing decisions with confidence.
Bearing Supplier Techniques That Ensure High Product Performance
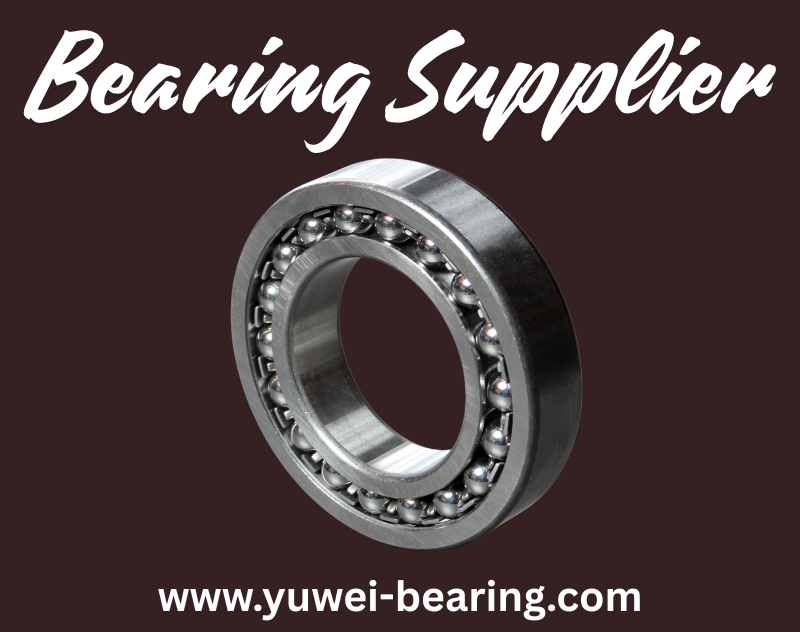
When it comes to ensuring the reliable operation of machinery, one of the most critical components is the bearing. The performance and longevity of these components often depend on the supplier’s manufacturing processes, quality control techniques, and attention to detail. A professional bearing supplier follows a set of industry-tested practices that guarantee high product performance.
This comprehensive guide covers the key techniques bearing suppliers use to deliver consistently high-quality bearings that meet strict industrial demands. Visit here!
Precision Manufacturing Processes
A bearing’s performance starts with how precisely it is manufactured. Precision in the dimensions, shape, and finish of each bearing component directly influences its ability to handle loads, reduce friction, and maintain stability under pressure.
- High-grade CNC machines are used for turning, grinding, and polishing to achieve micrometer-level tolerances.
- The roundness and flatness of races and rolling elements are maintained with high accuracy.
- Automated production systems minimize human error and increase repeatability.
- Laser measurement tools ensure consistent dimensional control throughout production.
Precision manufacturing eliminates minor variations that can lead to excessive wear, noise, and vibration.
Quality Raw Material Selection
Choosing the right material is foundational to bearing performance. A reliable bearing supplier carefully sources and verifies all raw materials before production.
- High-carbon chromium steel (e.g., 52100) is commonly used for its hardness and fatigue resistance.
- Stainless steel, ceramic, and hybrid materials are chosen based on specific application needs.
- Raw materials are tested for purity, microstructure, and mechanical properties before processing.
- Suppliers maintain full material traceability to ensure consistency and accountability.
Material quality directly affects durability, load capacity, and resistance to environmental factors.
In-House Heat Treatment
Heat treatment is essential for optimizing the hardness and internal structure of bearing steel. Suppliers that perform in-house heat treatment have better control over product quality.
- Heat treatment hardens the bearing surface while maintaining a tough core.
- Common methods include carburizing, through-hardening, and induction hardening.
- Parameters like temperature, duration, and atmosphere are tightly controlled.
- Uniform heat treatment improves wear resistance and reduces internal stress.
This step ensures the bearing maintains its properties under dynamic and static loads.
Contamination Control and Cleanroom Assembly
Even microscopic contaminants can compromise a bearing’s life. Clean environments and strict handling procedures are essential during assembly.
- Bearings are assembled in ISO-class cleanrooms to avoid dust and particles.
- Workers use gloves, gowns, and clean tools to prevent contamination.
- Bearings are vacuum-sealed or packaged with desiccants for long-term protection.
- Clean assembly reduces failures related to debris and corrosion.
Contamination control ensures longer operating life and reliable field performance.
Advanced Inspection and Testing
Quality bearings undergo thorough inspection and testing before being shipped. This ensures every bearing meets defined specifications.
- Visual and dimensional inspections verify physical conformance.
- Hardness and surface roughness are measured with precision tools.
- Advanced tests include vibration, noise (dB level), and torque analysis.
- Non-destructive testing (NDT) methods such as ultrasonic and magnetic particle tests detect internal flaws.
Inspection and testing confirm the integrity and reliability of each bearing unit.
Lubrication and Grease Management
Lubrication plays a vital role in reducing friction and preventing metal-to-metal contact. Suppliers handle lubrication based on the bearing’s end-use.
- Pre-lubricated bearings are filled with application-specific greases.
- The right amount of grease is injected using automated dispensers.
- Lubricants are selected based on speed, load, and temperature requirements.
- Seals are added to retain lubricant and keep contaminants out.
Proper lubrication enhances performance and minimizes maintenance needs.
Packaging and Storage Standards
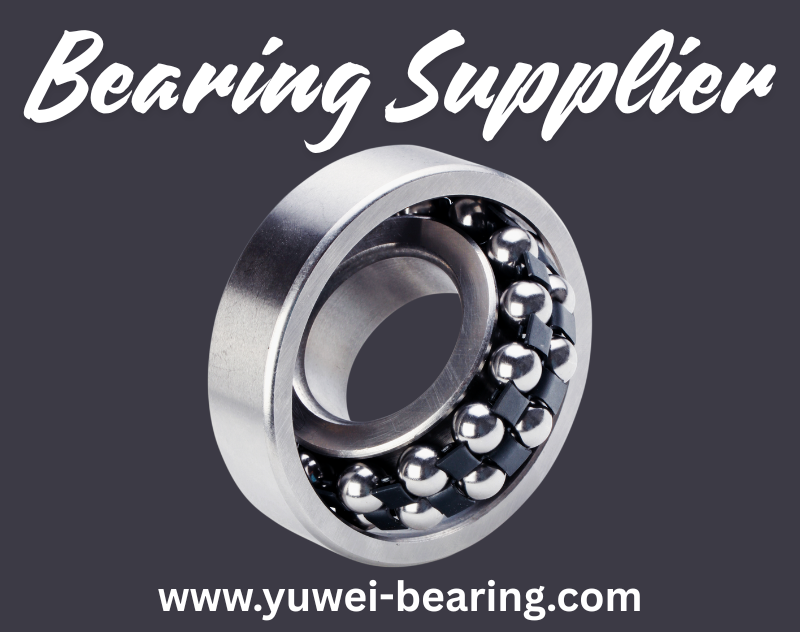
Packaging and storage can affect bearing quality during transportation and long-term storage.
- Bearings are packaged in anti-corrosive paper or vacuum-sealed plastic.
- Desiccants are included to control moisture.
- Temperature and humidity levels are monitored in storage facilities.
- FIFO (First In First Out) inventory practices ensure product freshness.
Good packaging preserves the bearing’s surface finish and lubrication integrity.
Traceability and Batch Control
Top suppliers implement full traceability systems to track every bearing batch from raw material to delivery.
- Each bearing is laser-etched with a batch number and code.
- Records include material certifications, process logs, and inspection results.
- Traceability supports quick recalls and root-cause analysis if needed.
This system improves quality control and accountability.
Technical Documentation and Compliance
Customers need assurance that bearings meet industry standards. Suppliers provide documentation to verify compliance.
- Certificates of Conformance (CoC) confirm manufacturing and material standards.
- Test reports and dimensional inspection sheets are available upon request.
- Compliance with ISO, ANSI, and customer-specific standards is documented.
This documentation supports audits, certifications, and regulatory requirements.
After-Sales Support and Performance Monitoring
A professional bearing supplier doesn’t stop at delivery. They offer support to ensure optimal bearing use in the field.
- Technical support teams assist with installation and troubleshooting.
- Bearing performance data may be collected and analyzed.
- Feedback loops help improve product design and application.
Ongoing support ensures customers get the best value and performance.
Summary Table: Bearing Supplier Techniques
Technique | Benefit |
---|---|
Precision Manufacturing | Low noise, high accuracy |
Quality Raw Materials | Longer life, better fatigue resistance |
In-House Heat Treatment | Optimized hardness, wear resistance |
Contamination Control | Reduced failure rates |
Advanced Testing | Verified performance, reliability |
Lubrication Management | Lower friction, minimal maintenance |
Secure Packaging | Protection during shipping and storage |
Traceability | Quality tracking and accountability |
Technical Compliance | Documentation for standards |
After-Sales Support | Field performance optimization |
Q&A Section
Q1: Why is traceability important in bearing supply?
Traceability allows suppliers and customers to track every bearing back to its origin. This ensures accountability, supports recalls, and helps maintain consistent quality.
Q2: What causes most bearing failures?
Common causes include contamination, improper lubrication, and overloading. Suppliers control these factors through clean assembly, grease selection, and precision manufacturing.
Q3: Can bearing suppliers customize products?
Yes, many suppliers offer customized bearings based on application-specific requirements such as size, load rating, materials, and lubrication.
Q4: How often should bearings be tested?
Every bearing is typically tested before shipment. Additional testing depends on application-criticality and customer specifications.
Q5: What standards should a bearing supplier meet?
Look for ISO 9001, ISO/TS 16949 (automotive), and specific industry standards like ASTM or ANSI depending on your sector.

Conclusion
Choosing the right bearing supplier is more than a purchasing decision—it’s a commitment to long-term performance, reliability, and operational efficiency. From raw material selection and precision manufacturing to advanced testing and contamination control, each process a supplier follows directly impacts how the bearing will perform in the real world. A trusted supplier doesn’t cut corners; they invest in cleanroom assembly, in-house heat treatment, and strict traceability systems to ensure each unit meets or exceeds quality expectations.
The best bearing suppliers also understand that their role doesn’t end at delivery. They offer after-sales support, technical guidance, and continuous improvement based on field feedback. This partnership approach helps businesses avoid costly downtime, increase machine longevity, and ensure smoother operations across the board.