In modern manufacturing and automation systems, precision is not optional—it’s essential. Industries like robotics, aerospace, automotive, and CNC machining all rely on components that can deliver high performance under demanding conditions. Among these critical components, cross roller bearing have become a go-to solution for engineers seeking accuracy, rigidity, and reliability in compact spaces. Unlike traditional bearings, cross-roller-bearings are designed to handle radial, axial, and moment loads simultaneously. This makes them ideal for applications such as robotic arms, CNC rotary tables, and medical imaging equipment, where multidirectional forces and precise movements are common.
As automation continues to evolve, the need for components that enhance both performance and efficiency grows stronger. Engineers and manufacturers are increasingly turning to cross roller bearings for their unique structure and performance advantages. From reducing backlash to increasing machine uptime, these bearings offer a clear competitive edge.
In this guide, we will explain everything you need to know about cross-roller-bearing—their design, benefits, applications, and how they contribute to enhanced performance in robotic arms and CNC machines.
Cross Roller Bearing Enhanced Performance in Robotic Arms and CNC Machines
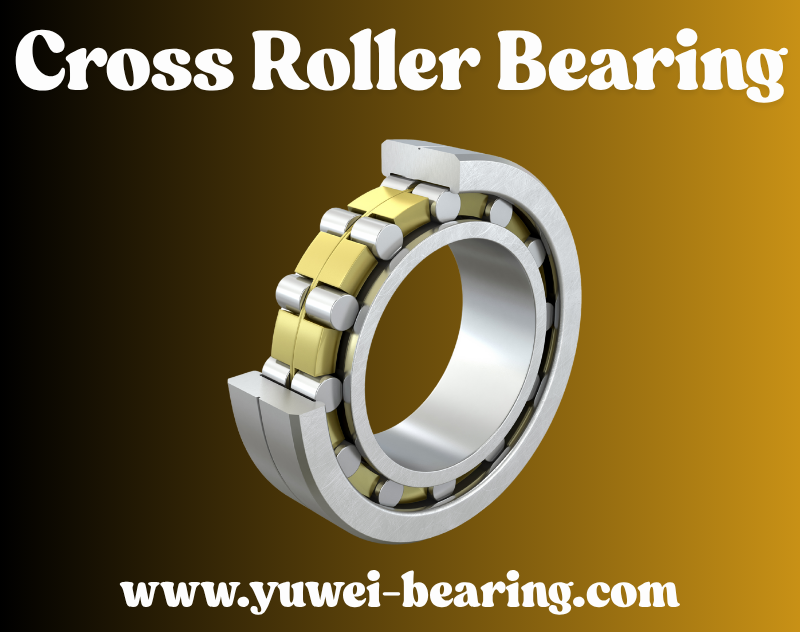
In today’s manufacturing and automation industries, precision isn’t just a requirement—it’s the baseline. Whether it’s robotic arms assembling intricate electronic components or CNC machines carving metal down to the micron, these systems demand consistent, multidirectional load capacity and zero tolerance for backlash.
Yet, many engineers and manufacturers still face limitations with conventional bearing setups. Traditional ball or roller bearings may perform well under single-direction loads, but once both axial and radial forces come into play, performance degrades. Misalignments creep in. Vibration increases. Output accuracy dips. Over time, this leads to more than just machine wear—it leads to production delays, inconsistent product quality, and rising maintenance costs. Visit here!
That’s the challenge. The market demands motion systems that can handle complex, high-precision tasks without performance decay.
What’s Aggravating the Issue?
The increasing use of high-speed robotic automation and multi-axis CNC machining has pushed the limits of conventional mechanical components. Consider these realities:
- Robotic arms are now required to perform ultra-precise pick-and-place tasks at incredible speeds, sometimes exceeding 100 picks per minute.
- CNC machines, particularly in the aerospace and medical industries, demand surface finishes within sub-micron tolerances—where even a minor vibration can ruin a workpiece.
- Load directions are no longer predictable. Tools and end-effectors rotate, tilt, and shift dynamically, applying force in multiple directions at once.
Most standard bearing setups—whether angular contact bearings, ball bearings, or tapered rollers—aren’t designed to take on these combined loads without compromise. As the machine’s speed and complexity increase, these bearings struggle, leading to:
- Increased maintenance intervals
- Higher downtime costs
- Cumulative tolerance stack-up
- Poor repeatability in production cycles
This is where cross-roller-bearing start to prove their worth—not with flair, but with solid, data-backed performance.
Solution: Cross Roller Bearings Deliver Where Others Fall Short
What Is a Cross Roller Bearing?
A cross roller bearing is a compact bearing designed to handle radial, axial, and moment loads simultaneously. Unlike traditional bearings where rollers are arranged in a single orientation, cross roller bearings use alternating orthogonal cylindrical rollers positioned at 90° angles to each other within a single raceway.
This unique configuration offers several tangible advantages:
- High rigidity due to preloaded rollers
- Minimal frictional resistance even under heavy loads
- Compact design, reducing equipment footprint
- Excellent rotational accuracy, ideal for high-precision tasks
Unlike conventional bearings which often require multiple components to handle different directions of force, a single cross-roller-bearing can do the job—cutting down on space, complexity, and long-term maintenance.
Proof: Real-World Case Studies That Back the Claims
Let’s dive into real-world examples where cross roller bearings were integrated into robotic arms and CNC machinery, and how they transformed performance:
Case Study 1: Robotic Arm Assembly Line – China Electronics Manufacturer
Background:
A leading electronics company in China operates a fully automated robotic arm assembly line producing LCD displays. Each robotic arm performs micron-level placement of fragile glass panels.
Problem:
Their prior setup involved dual angular contact ball bearings in each joint. While functional, these bearings suffered from gradual misalignment and required recalibration every 3 months. The system faced:
- Positional drift of up to ±0.015 mm
- Vibration spikes that affected sensor calibration
- Downtime of 14 hours/month for maintenance
Solution:
The engineering team replaced the existing bearing sets with cross-roller-bearings in the robot’s rotational joints.
Result:
- Positional accuracy improved to ±0.005 mm
- Maintenance dropped to a single yearly service
- System uptime improved by 26% annually
- Cost savings of $47,000/year in reduced maintenance and recalibration downtime
Case Study 2: CNC Milling Machine – Precision Aerospace Parts
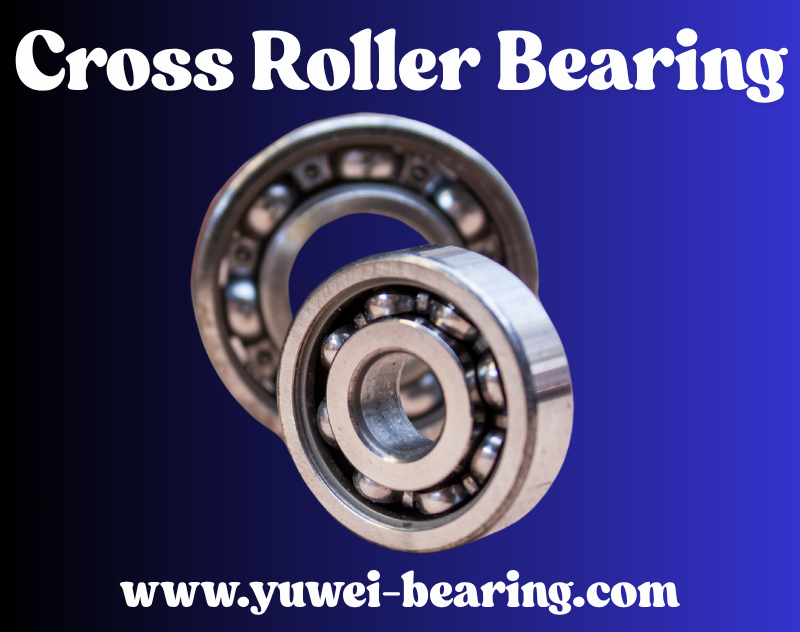
Background:
An aerospace supplier in China needed tighter tolerances for aluminum and titanium components in their 5-axis CNC milling machines.
Problem:
Even small amounts of tool deflection or spindle backlash were causing surface finish errors, leading to reworks. The root cause? The spindle’s conventional bearing system couldn’t handle combined axial and radial loads during complex angular milling.
Solution:
Cross-roller-bearing were integrated into the spindle housing.
Result:
- Vibration reduced by 38% during high-speed rotation
- Surface finish tolerance improved by 21%
- Part rejection rate dropped by over 50%
- Machine uptime increased by 12% per quarter
Deeper Dive: Why Cross Roller Bearings Outperform
1. Single Bearing, Multi-Directional Load Handling
Cross roller bearings eliminate the need for stacking multiple bearing types to handle different loads. This not only simplifies design but reduces potential points of failure and tolerance misalignment.
2. High Rigidity in Minimal Space
The alternating roller design allows for much tighter contact with the raceway, enabling a higher rigidity ratio than ball bearings of similar size. This is essential for robotic arms working with sensitive sensors or CNC machines machining tight curves.
3. Preload Capabilities
Cross roller bearings can be preloaded during assembly. This means backlash is virtually eliminated, an essential requirement for repeatable, accurate motion—especially in robotic joint mechanisms and CNC spindles.
4. Greater Service Life
Because the load is distributed across a wider area (thanks to cylindrical rollers), wear is slower and more uniform. Combined with their enclosed, often maintenance-free design, this adds to the bearing’s operational lifespan.
How Cross Roller Bearings Fit Into System Design
In Robotic Arms
- Joint articulation: Typically used in rotary joints, where precision rotation is key
- End-effector stability: Ensures tools and sensors are perfectly aligned
- Reduced inertia: Smaller bearing size leads to lighter arms and faster acceleration
In CNC Machines
- Rotary tables: Enhanced stability under combined loads improves cut accuracy
- Spindles: Handles cutting forces while maintaining exact rotational positioning
- Indexing heads: Helps in high-speed rotation with minimal lag or vibration
Considerations Before Choosing Cross-Roller-Bearing
While cross roller bearings offer significant benefits, it’s important to evaluate the following factors for proper integration:
- Load Requirements: Understand the radial, axial, and moment loads across all operating conditions.
- Operating Environment: Cross roller bearings can be sealed and lubricated for cleanroom or high-dust applications.
- Precision Class: Choose from standard (P0) to ultra-precision (P2) depending on application needs.
- Mounting and Preload Options: Work with bearing suppliers to customize preload levels and ensure proper mounting torque.
🔧 Frequently Asked Questions About Cross Roller Bearing
Q1: What makes a cross-roller-bearing different from traditional bearings?
A: Unlike traditional bearings that use balls or single-direction rollers, cross-roller-bearing have cylindrical rollers arranged at 90° angles in an alternating pattern. This design allows them to support radial, axial, and moment loads simultaneously, which simplifies the mechanism and boosts precision.
Q2: Where are cross-roller-bearings typically used?
A: Cross-roller-bearing are commonly used in applications requiring high rigidity and precision, such as robotic arms, CNC rotary tables, indexing heads, medical imaging equipment, and aerospace positioning systems.
Q3: Can cross-roller-bearing reduce machine vibration and backlash?
A: Yes. Due to their high rigidity and ability to be preloaded, cross-roller-bearing significantly reduce backlash and absorb vibrations better than conventional bearings. This results in more stable, accurate movement, especially in high-speed or high-load applications.
Q4: Are cross-roller-bearing difficult to install or maintain?
A: Not at all. Many models come as integrated units with mounting holes, making installation straightforward. Additionally, because they handle multiple load directions in a single unit, they reduce the number of components and are often sealed for long maintenance-free operation.
Q5: How do I choose the right cross-roller-bearing for my application?
A: Selection depends on factors like load direction and magnitude, required accuracy, available space, and environmental conditions. It’s best to consult with a bearing manufacturer or specialist to determine the optimal size, preload, and material for your specific use case.
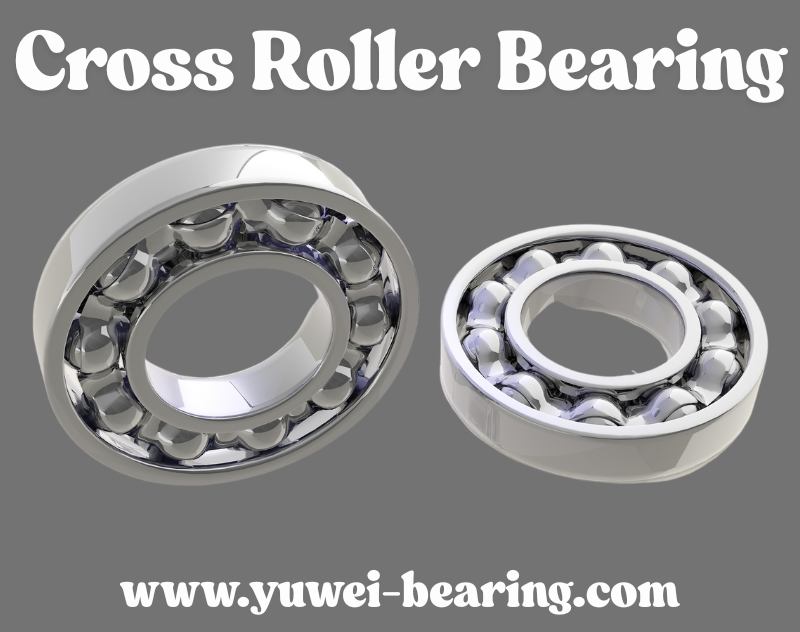
Conclusion
Cross roller bearing have proven themselves as a critical innovation in the pursuit of precision, efficiency, and durability in modern machinery. Their ability to handle complex, multidirectional loads within a compact form factor makes them especially valuable in high-performance environments like robotic arms and CNC machines. By integrating cylindrical rollers at right angles, these bearings provide unmatched rigidity, reduce backlash, and ensure stable, accurate motion even under heavy operational demands.
Industries that rely on high-speed, high-accuracy equipment—such as aerospace, medical, semiconductor, and advanced manufacturing—are increasingly adopting cross-roller-bearing to enhance overall system performance. From reducing maintenance intervals to improving repeatability and part quality, the real-world advantages are both measurable and significant.
As machines become more compact yet more capable, the components that drive them must also evolve. Cross-roller-bearing represent that evolution—bridging the gap between precision engineering and real-world durability. Whether you’re designing new automation systems or upgrading existing equipment, investing in the right bearing technology can deliver long-term performance and reliability.
Choosing cross-roller-bearing is not just a component upgrade—it’s a strategic decision toward higher operational excellence and reduced downtime.