Heavy machinery is built to endure brutal conditions — crushing loads, non-stop vibrations, dirt, moisture, and extreme temperatures. But beneath all that steel and power lies one critical component that keeps it all moving smoothly: the roller bearing. While small in size compared to the massive machines they support, roller bearings are essential to maintaining functionality, reliability, and safety in industrial operations.
From mining trucks to construction excavators and manufacturing systems, roller-bearings absorb tremendous radial and axial forces, allowing these machines to operate continuously under pressure. Their durability directly affects equipment uptime, maintenance costs, and even worker safety. When bearings fail, the ripple effect can mean thousands in lost productivity and hours of unplanned downtime.
But not all roller-bearings are created equal. Their strength and lifespan depend heavily on design, load capacity, material quality, and environmental fit. Understanding how they work — and how to choose the right one — can be the difference between peak performance and frequent breakdowns.
In this guide, we will explain the strength and durability of roller bearings in heavy machinery, backed by real-world case studies, technical facts, and practical advice.
Roller Bearing Strength and Durability in Heavy Machinery
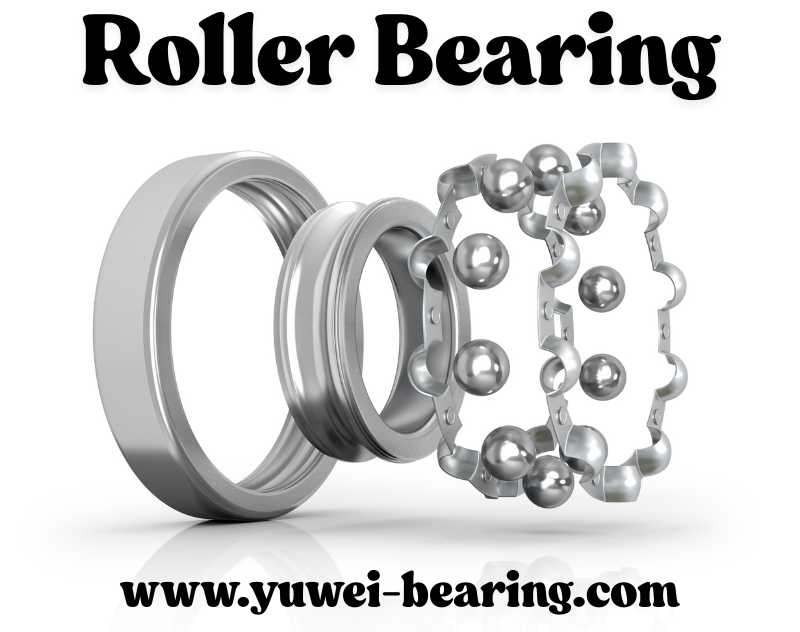
In the world of heavy-duty machinery — from construction excavators to mining trucks and steel mills — performance isn’t just about horsepower or design. It’s about what holds the machine together under pressure. And that’s where roller bearings come into play.
These components might look small compared to the giants they support, but roller-bearings are responsible for handling some of the most extreme conditions in the industrial sector. They carry massive loads, rotate at high speeds, and endure harsh environments — day in and day out. Visit here!
If you want equipment that lasts and performs reliably, understanding the strength and durability of roller-bearing isn’t optional — it’s essential.
Problem: When Failure Isn’t an Option
Heavy machinery operates under constant stress — axial loads, radial loads, vibrations, misalignment, high temperatures, and dirty conditions. When a component fails, it can bring operations to a halt, leading to:
- Unplanned downtime
- Expensive repairs
- Safety hazards
- Lost productivity
A 2023 report by Plant Engineering Magazine revealed that bearing failures account for up to 51% of mechanical equipment breakdowns in industrial settings. That’s more than half. And most of those failures stem from poor load handling, contamination, and improper bearing selection or lubrication.
Roller bearings aren’t invincible — but when chosen wisely and maintained correctly, they can withstand some of the toughest working conditions known to man.
Solution: Why Roller Bearings Are Built for the Heavy Stuff
Roller bearings are designed specifically for high-load applications. Their rolling elements (cylindrical, spherical, tapered, or needle-shaped) allow them to carry heavier loads than traditional ball bearings. Here’s how:
1. Larger Contact Area
Unlike ball bearings that contact at a single point, roller-bearings have line contact between rolling elements and raceways. This spreads the load over a larger area, reducing stress and increasing capacity.
2. Load Capacity
Roller bearings can handle:
- High radial loads (in cylindrical roller designs)
- Combined radial and axial loads (in tapered or spherical roller-bearings)
- Shock loads (in heavy industrial applications)
For instance, spherical roller bearings used in mining conveyors regularly endure shock loads exceeding 1500 kN.
3. Material Strength
Most roller bearings are made from high-grade chromium steel (e.g., AISI 52100), with surface treatments like carburization or case hardening. These materials provide:
- High fatigue resistance
- Wear protection
- Long service life
Case Study: SKF Bearings in Iron Ore Mining
Let’s look at a real-world example.
Challenge: A leading iron ore mining company in Western Australia was experiencing frequent breakdowns in its conveyor pulley systems. Bearings were failing every 4–6 months due to heavy shock loads, high dust contamination, and poor lubrication conditions.
Solution: The company switched to SKF Explorer spherical roller-bearing with sealed units and a high-load design.
Results:
- Bearing lifespan increased from 4 months to over 2 years
- Downtime reduced by 70%
- Maintenance costs decreased by $150,000 annually
- Improved safety by reducing need for manual inspections in hazardous zones
This case shows what happens when the right roller-bearing is used for the job: fewer breakdowns, more uptime, and direct cost savings.
Types of Roller-Bearings and Their Heavy Machinery Roles
Each type of roller-bearing is designed with a different load and motion profile in mind. Here’s a quick breakdown of where they shine in heavy equipment:
1. Cylindrical Roller-Bearings
- Application: Gearboxes, electric motors, steel mills
- Strength: High radial load capacity, fast speeds
- Limitation: Limited axial load support
2. Spherical Roller-Bearings
- Application: Mining conveyors, vibrating screens, crushers
- Strength: Self-aligning, handle heavy radial and axial loads, resist misalignment
- Durability Factor: Suitable for contaminated environments
3. Tapered Roller-Bearings
- Application: Axle systems, construction vehicles, loaders
- Strength: Manage both radial and axial loads
- Durability Factor: Widely used in mobile heavy equipment due to rugged performance
4. Needle Roller-Bearings
- Application: Hydraulic pumps, transmissions
- Strength: Compact, high load in limited space
- Durability Factor: Best where space-saving is crucial
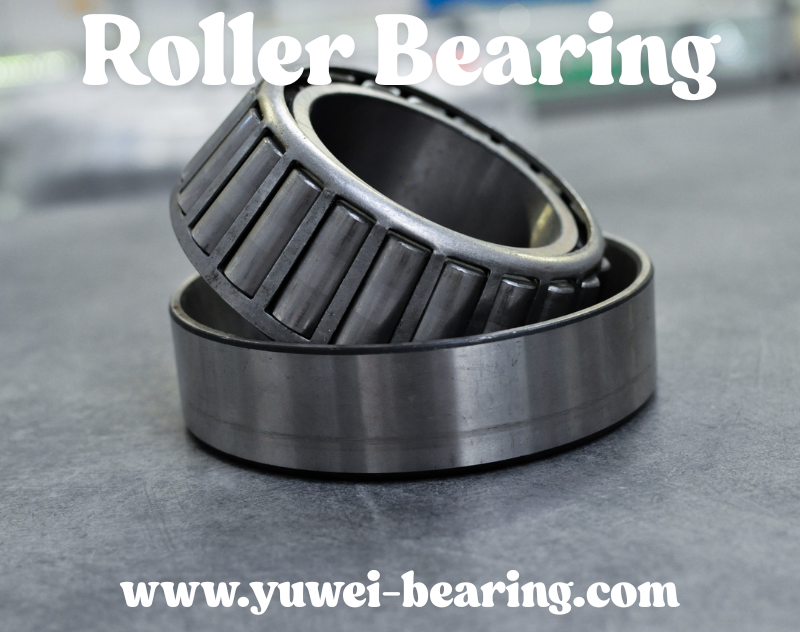
Durability Factors: What Makes Roller-Bearing Last
Durability isn’t just a result of strong materials. It’s the outcome of precision engineering, smart design, and maintenance practices. Here’s what contributes most to roller-bearing life:
1. Correct Load Matching
Using a bearing rated for the actual load is critical. Underestimating loads leads to fatigue and early failure. Over-engineering may result in higher costs with no added benefit.
2. Lubrication
According to a 2022 study by the Society of Tribologists and Lubrication Engineers (STLE), improper lubrication causes 36% of bearing failures. Modern lubrication solutions include:
- Automatic lubrication systems
- Grease with solid additives (for extreme loads)
- Oil bath lubrication (for enclosed systems)
3. Contamination Control
Heavy machinery works in gritty environments — mud, water, metal dust. Seal design (contact or non-contact) plays a huge role in bearing longevity. Proper housing and protective covers also reduce the entry of harmful particles.
4. Precision Installation
Using tools like hydraulic sleeves, induction heaters, and torque-controlled tools during installation ensures proper fit and avoids raceway damage.
Real Cost of Downtime: A Quick Math
Let’s quantify durability with simple numbers.
A manufacturing plant running a $2 million extrusion line loses around $8,000 per hour of unplanned downtime. If a failed roller-bearing stops the machine for just 12 hours:
- Downtime cost = 12 × $8,000 = $96,000
- Replacement bearing = ~$1,200
- Total maintenance team cost = ~$3,500
Net Loss: Over $91,000 because of one compromised bearing.
Now imagine multiplying that across a year or across several machines. That’s why companies are moving toward predictive maintenance and high-quality bearing investments.
Emerging Tech: Smart Bearings and IoT Integration
Modern heavy machinery is evolving, and so are roller bearings.
Companies like Timken, Schaeffler, and NSK are now offering sensor-integrated roller-bearings that monitor:
- Temperature
- Vibration
- Load
- RPM
When combined with machine learning or predictive analytics, these smart systems warn of fatigue or contamination before failure happens. It’s proactive durability in action.
Maintenance Best Practices: Get the Most from Your Bearings
If you want roller-bearing to live up to their potential, here are practical tips:
- Match the Bearing to the Application: Use load, speed, and environment data for selection.
- Monitor Lubrication: Use the right type, apply it regularly, and monitor viscosity.
- Keep It Clean: Avoid contamination during handling, installation, and operation.
- Use Proper Tools: Avoid hammering bearings or using makeshift tools.
- Inspect Regularly: Vibration and temperature trends tell a lot about bearing health.
Industry Adoption: Why Big Brands Stick With Roller-Bearing
Major manufacturers and users of heavy machinery — including Caterpillar, Komatsu, John Deere, and Volvo CE — rely on roller bearings because of their:
- Proven performance in rugged environments
- Load-handling efficiency
- Customizability for different machine specs
These companies often partner with bearing makers to design custom solutions based on machine use profiles, further enhancing strength and durability.
🔧 Roller Bearing FAQs: What You Need to Know
1. What makes roller-bearings suitable for heavy machinery?
Roller-bearing are designed to support large radial and axial loads due to their line contact between the rolling element and raceway. This design spreads pressure across a larger surface, reducing stress and increasing load-bearing capacity. This makes them ideal for heavy-duty applications like construction, mining, and industrial manufacturing.
2. How long do roller-bearings typically last in industrial environments?
Lifespan varies based on load, speed, lubrication, and environmental conditions. However, with proper maintenance and quality materials, roller-bearing in heavy machinery can last 5 to 10 years or longer. Case studies in mining operations have shown lifespan increases from 4 months to over 2 years after switching to high-performance bearings with improved sealing and lubrication.
3. What are the most common reasons roller bearings fail?
The top causes of roller-bearing failure include:
- Improper lubrication (36% of failures)
- Contamination from dirt or metal particles
- Overloading beyond rated capacity
- Misalignment or poor installation
- Fatigue from extended use under vibration
Regular inspection and correct installation are key to preventing these issues.
4. Can roller bearings handle both radial and axial loads?
Yes — but the ability depends on the bearing type:
- Cylindrical roller-bearing handle high radial loads only.
- Tapered and spherical roller-bearings handle both radial and axial loads.
Selecting the right type based on machine load direction is essential for performance and durability.
5. Are sealed roller-bearings better for dirty or outdoor environments?
Absolutely. Sealed roller-bearings prevent entry of contaminants like dust, mud, or water — common in construction and mining. Sealing reduces the need for frequent re-lubrication and protects the internal components, extending service life significantly.
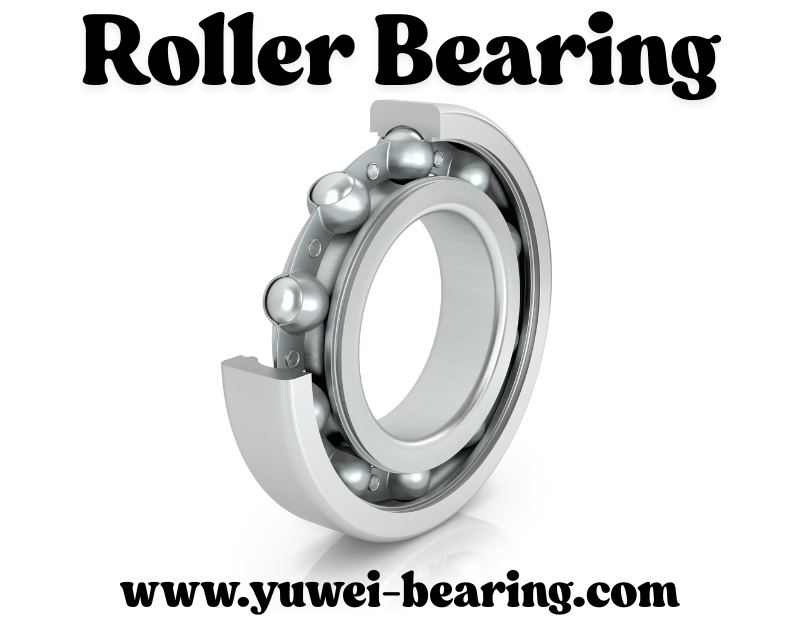
Conclusion
Roller bearing may be small, but their role in heavy machinery is massive. They carry the weight — literally — of industries that depend on reliable, continuous operation. Whether in mining, construction, manufacturing, or power generation, these components are responsible for reducing friction, absorbing loads, and keeping equipment running smoothly under extreme conditions.
As we’ve explored, the strength of roller-bearings lies in their design — line contact for better load distribution, robust materials for fatigue resistance, and precision engineering for long-term durability. But strength alone isn’t enough. Choosing the right bearing for your application, ensuring proper installation, and following strict maintenance routines are just as critical to maximizing bearing life and minimizing downtime.
Case studies show it clearly: when companies invest in the right roller-bearing solutions, they save money, improve safety, and avoid costly operational disruptions.
In industries where failure is not an option, understanding and prioritizing roller-bearing performance is not just a technical detail — it’s a strategic decision. Choose smart, maintain well, and your heavy machinery will return the favor with years of dependable service.