In high-performance industries like robotics, aerospace, and advanced manufacturing, even the smallest component can determine the success or failure of an entire system. Bearings, often overlooked, are critical to the movement, stability, and longevity of machinery. Yuwei Bearing has emerged as a trusted name in this field by focusing on what truly matters—quality. With years of expertise, modern production facilities, and a commitment to precision engineering, Yuwei Bearing delivers products that meet the demanding requirements of global industries.
What sets Yuwei apart is not just its product range, but its approach to quality assurance. Every bearing is manufactured using certified raw materials, precision-machined with advanced equipment, and thoroughly tested before delivery. Cleanroom assembly, strict dimensional checks, and dynamic performance testing are just part of the rigorous steps in their production chain. The result is a bearing that performs reliably in harsh conditions and complex applications.
In this guide, we will explain how Yuwei Bearing ensures reliability through its structured and proven quality assurance process.
Yuwei Bearing – Reliable Products Built Through Quality Assurance
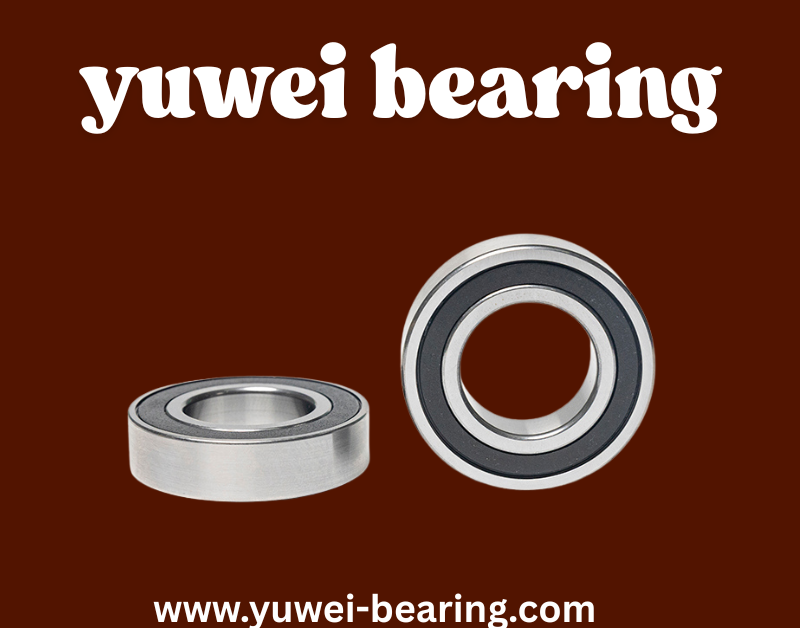
When it comes to industrial machinery, the smallest component can be the key to consistent performance. Bearings, in particular, are foundational to everything from robotics and wind turbines to CNC machines and construction equipment. Yuwei Bearing, a leading manufacturer in the field, has built its reputation not through flashy marketing, but through a commitment to quality that shows in every unit it produces. This article dives deep into how Yuwei Bearing ensures reliability, and how quality assurance processes form the core of its production ecosystem. Visit here!
The Industrial Backbone: Why Bearing Quality Matters
Bearings support motion, reduce friction, and carry loads. A poorly made bearing can cause machine failure, halt production lines, and trigger expensive downtime. In industries where precision and uptime are critical, reliability is not negotiable.
According to a 2023 survey published by the Industrial Motion Research Institute, over 68% of machinery breakdowns in automated factories were traced back to substandard bearing performance. This statistic alone explains why manufacturers, suppliers, and OEMs are shifting toward proven, quality-verified bearing brands like Yuwei.
Overview of Yuwei Bearing’s Operations
Yuwei Bearing, headquartered in China, specializes in precision bearings including crossed roller bearings, thin-section bearings, and custom-engineered bearing systems. The company serves sectors such as:
- Robotics and automation
- Aerospace and defense
- Medical imaging devices (e.g., CT scanners)
- Machine tools
- Energy (wind and solar)
Rather than trying to cover every bearing type, Yuwei focuses on niche markets that demand tighter tolerances and higher rotational accuracy.
With over 15 years in operation, Yuwei exports to more than 30 countries, and it operates multiple production plants that are ISO 9001 and IATF 16949 certified. The company employs a team of mechanical engineers, quality control professionals, and R&D specialists who work in tandem to ensure every batch meets performance expectations.
Yuwei’s Quality Assurance Process – A Ground-Level Breakdown
Let’s walk through how a typical Yuwei Bearing is developed and tested. The goal isn’t just meeting the standard – it’s to exceed it with repeatable precision.
1. Raw Material Inspection
Before production begins, incoming steel undergoes rigorous metallurgical testing. Yuwei sources its materials from approved mills in Japan and Germany, known for consistent alloy properties.
Each steel batch is tested for:
- Hardness (HRC)
- Chemical composition (using spectrometers)
- Grain structure (via microscopic inspection)
In 2022, Yuwei rejected 4.1% of incoming steel batches—indicating a strict zero-compromise approach.
2. Precision Machining
Bearings are precision-ground using multi-axis CNC equipment. Dimensional tolerances as tight as ±0.002 mm are achieved. For thin-section and crossed roller bearings, roundness, flatness, and parallelism are critical to ensure load distribution.
During this phase:
- Operators use digital micrometers and laser scanners to verify dimensions.
- In-line measurement systems reduce human error.
Yuwei recently upgraded its grinding line with equipment from Okuma and Schneeberger, reducing production time by 17% while maintaining accuracy levels.
3. Heat Treatment and Stabilization
To enhance durability, bearing components undergo vacuum heat treatment. The process improves core hardness while maintaining surface ductility.
- Yuwei uses a multi-zone vacuum furnace system.
- Components are stress-relieved post-treatment to prevent warping.
According to a 2023 internal audit, the failure rate due to post-assembly distortion dropped from 1.7% to 0.4% after the stabilization phase was optimized.
4. Clean Room Assembly
One often-overlooked factor in bearing quality is contamination. Even a micron-level speck of dust can compromise performance in high-speed or high-load applications.
At Yuwei, assembly takes place in ISO Class 7 clean rooms. Personnel wear full-body protective gear, and automated robotic arms handle lubrication and cage assembly. Torque resistance and rotational accuracy are tested in real-time.
Case Study Example:
In 2021, a South Korean CNC manufacturer reported premature bearing wear in their tool spindles. After switching to Yuwei’s clean room-assembled bearings, bearing life increased by 28%, and spindle maintenance dropped from every 6 months to once annually.
5. Dynamic Testing and Simulation
Beyond static measurements, bearings are tested in simulated operational conditions.
Tests include:
- Life-cycle testing (run to failure under standard load)
- Vibration analysis
- Load-to-failure compression testing
- Low-speed and high-speed rotation consistency
One of Yuwei’s key facilities includes a dynamic testing chamber capable of simulating -40°C to +120°C temperature ranges—relevant for aerospace and arctic applications.
Results are documented digitally and stored for seven years. This traceability has become a strong selling point for Yuwei when bidding for government and military contracts.
Certifications and Industry Compliance
Yuwei’s plants are certified to:
- ISO 9001: Quality management systems
- IATF 16949: Automotive industry standards
- ISO 14001: Environmental management
Yuwei bearings also conform to RoHS and REACH requirements, making them suitable for the EU and North American markets.
In 2023, the company passed a rigorous 3rd-party audit conducted by TÜV Rheinland with a compliance score of 98.7%. This audit included document traceability, in-process defect tracking, and customer feedback response metrics.
Customer-Centric Adjustments: Real-World Reliability
One of the most practical demonstrations of quality comes from customer case studies.
Case Study: Wind Turbine Manufacturer in Denmark
A major wind turbine OEM had been struggling with bearing fatigue in their yaw control systems. Their existing supplier could not offer traceable quality reports nor provide consistent delivery schedules. After a 6-month pilot program with Yuwei’s customized cross-roller bearings:
- Maintenance intervals extended from 18 to 30 months
- Load deflection dropped by 12%
- Bearing failure rate reduced to less than 0.5% across 400+ turbines
Yuwei’s engineers worked closely with the client, tweaking preload values and bearing cage design to meet rotational stability requirements under wind gust load profiles.
This success story was published in the 2023 Renewable Systems Engineering Journal, further validating Yuwei’s practical reliability.
Continuous Improvement Through Feedback Loops
Quality assurance is not a one-time checklist at Yuwei—it’s an evolving loop. After every client delivery, the following data is collected:
- On-site performance reports
- Failure analysis, if any
- Shipping damage checks
- Customer support interaction reviews
Every quarter, Yuwei conducts an internal Kaizen (improvement) session where customer feedback is presented alongside defect and downtime statistics. In 2024, changes driven by this process led to a 13% increase in assembly speed and a 9% drop in customer-reported defects.
Transparent Delivery and Traceability
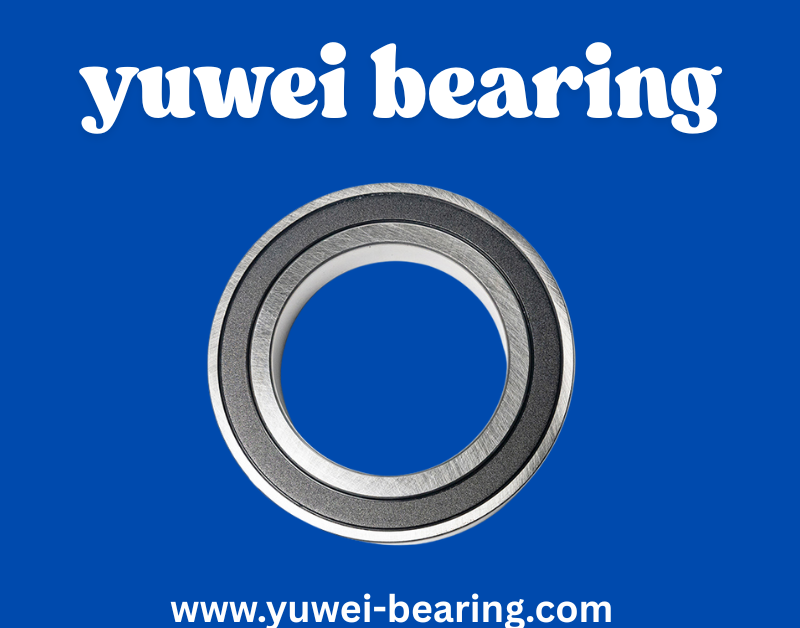
Even the best product is worthless if it doesn’t arrive on time or cannot be traced back to its origin. Yuwei maintains a digital dashboard where customers can:
- Track production status in real time
- View QA reports for their batch
- Download CAD files and spec sheets
- File support tickets directly to engineering teams
This system has cut down order-related disputes by 31% in the past year and improved order-to-ship cycle time from 21 days to 14 days for high-priority clients.
Why Engineers and OEMs Trust Yuwei Bearing
Here’s what separates Yuwei from many competitors:
Feature | Yuwei Bearing | Typical Supplier |
---|---|---|
Material Sourcing | Certified mills (Japan, Germany) | Local unverified mills |
Cleanroom Assembly | ISO Class 7 | Basic workshop |
Traceability | Digital logs, 7-year records | Manual logs or none |
Customization | Engineering collaboration | Standard sizes only |
Failure Rate | <0.5% (2024 data) | 2-3% industry average |
Certification | ISO 9001, IATF 16949, RoHS | Partial or none |
Thoughts
Reliability isn’t a matter of branding or slogans—it’s the result of every small decision made in sourcing, machining, testing, and service. Yuwei Bearing has built a process that puts data, testing, and feedback before shortcuts. The result? Bearings that perform under pressure, last longer, and reduce maintenance costs in real-world industrial environments.
In a market where many suppliers compete on price, Yuwei competes on accountability. And in today’s industry, that’s the kind of reliability buyers are willing to invest in.
Frequently Asked Questions About Yuwei Bearing
1. What types of bearings does Yuwei Bearing manufacture?
Yuwei Bearing specializes in precision bearings such as crossed roller bearings, thin-section bearings, and customized bearing solutions for high-performance applications including robotics, aerospace, and industrial automation.
2. How does Yuwei ensure the quality of its bearings?
Quality is maintained through a multi-step assurance process including raw material testing, precision machining, cleanroom assembly, and dynamic performance testing. Every bearing is tracked and documented for full traceability.
3. Are Yuwei bearings certified for international use?
Yes. Yuwei products are manufactured under ISO 9001 and IATF 16949 certified systems and comply with RoHS and REACH standards, making them suitable for international markets including Europe, North America, and Asia.
4. Where are Yuwei Bearing products made?
Yuwei’s manufacturing plants are located in China and are equipped with modern CNC machinery, vacuum heat treatment systems, and ISO Class 7 cleanroom assembly lines.
5. Can Yuwei bearings be customized for specific industrial needs?
Yes. Yuwei works closely with OEMs and engineering teams to develop custom solutions, including tailored preload values, cage designs, and mounting options.
Conclusion
Yuwei Bearing has built its reputation on a foundation of precision, reliability, and strict quality assurance. From raw material inspection to final product testing, every step in their production process is engineered for consistency and long-term performance. By using advanced machinery, cleanroom assembly environments, and internationally certified systems, Yuwei ensures that each bearing meets or exceeds industry standards. Their attention to detail doesn’t stop at manufacturing—customer feedback, traceability systems, and after-sales support are all integrated into their quality framework.
Industries that rely on high-performance components—such as robotics, CNC machining, and renewable energy—continue to choose Yuwei not just for their products, but for the peace of mind that comes with them. The company’s low failure rate, responsive engineering support, and transparent communication have helped it stand out in a highly competitive global market.
Choosing Yuwei Bearing means investing in a product that has been tested, verified, and built to deliver under pressure. It’s a commitment to performance and trust that goes beyond price and packaging—and one that continues to earn respect from engineers and OEMs worldwide.